Bei der Lötmaskenanwendung dreht sich alles um das Lötmaskenmaterial. Dennoch sollte die Aufmerksamkeit nicht allein auf das Material gerichtet werden. Die mit dem Tintenstrahldrucker gedruckte Lötstoppmaskenschicht besteht aus einer Ansammlung von Tropfen; neben der Lötstoppmaskentinte spielen noch einige andere Materialien eine Rolle bei der Formung dieser Tropfen.
Meine vorherige Spalte der Positionierung des Tropfens große Aufmerksamkeit gewidmet. Ebenso wichtig wie die Position ist jedoch die Art und Weise, wie der fliegende Tropfen nach dem Aufsetzen auf dem Untergrund seine endgültige Form erreicht. Der Querschnitt dieser Form (Abbildung 1) und insbesondere die Ränder sind das Ergebnis eines Gleichgewichts. Die Kontaktwinkeltheorie beschreibt es. Der interessante Haken an der Sache ist, dass drei Aggregatzustände beteiligt sind und daher eine große Anzahl von Materialien den Tropfen beeinflussen. Selbst ein virtueller, digitaler Zustand der Materie spielt eine Rolle.
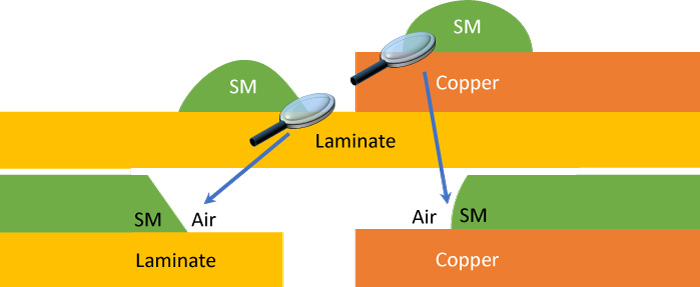
Abbildung 1: Skizze mit Tropfen auf verschiedenen Materialien.
Der Tropfen findet in seinem flüssigen Zustand eine Gleichgewichtsposition auf einem Festkörper, dem Substrat. Die Vorhersagbarkeit dieses Gleichgewichts ist ein Kernparameter des Tintenstrahldrucks. Sie ist ausschlaggebend für die Fähigkeit, ein Muster mit hoher Wiedergabetreue zu reproduzieren. Für Physikliebhaber gibt es reichlich Literatur, die erklärt, warum, was und wie sich dieses Gleichgewicht einstellt. Für den Bereich der Reproduzierbarkeit reicht es aus, die beteiligten Materialien zu betrachten: Luft, das Farbmaterial und den Bedruckstoff. Letzterem muss besondere Aufmerksamkeit gewidmet werden, da jeder Bedruckstoff in Bezug auf Topographie und Material variiert.
Luft ist das am einfachsten zu behandelnde materielle Element und sollte nicht als selbstverständlich angesehen werden. Die Aufmerksamkeit richtet sich auf Schwebeteilchen und Luftströmungen. Erstens, wenn sich die Tropfen zufällig auf der Lötmaskenschicht absetzen, wird der Kontaktwinkel stark gestört. Eine Überlegung und zwei Aktionspunkte verhindern Probleme. Nur große Partikel von mindestens einigen Mikrometern Größe verursachen tatsächlich Probleme. Das ist eine Erleichterung, denn die jahrzehntelange Erfahrung der Halbleiterindustrie bei der Kontrolle von Partikeln ist vorhanden, um mit solchen Größen umzugehen.
Von den Überlegungen zu den Maßnahmen: Die erste Maßnahme findet außerhalb des Tintenstrahldruckers statt, eine Nassreinigung befreit die Oberfläche der Eingangsplatte von Verunreinigungen wie Partikeln und organischen Verschmutzungen. Die zweite Maßnahme stellt sicher, dass die interne Umgebung des Druckers mindestens ISO 5 (Klasse 100) aufweist. Die Abwesenheit von Menschen in der internen Umgebung vereinfacht das Funktionsdesign für diese Spezifikation, da sie die größte Quelle für Partikel sind. Außerdem setzt diese Spezifikation voraus, dass jederzeit ein langsamer, homogener Strom sauberer Luft vorhanden ist. In Verbindung mit der richtigen Anordnung und Bewegung der Druckköpfe führt dies zu vorhersehbaren Luftströmen, mit denen der Druckkopf die Tropfen abgibt.
Der Festkörper (das Substrat) kann auf verschiedene Arten auftreten. Laminate und Kupfer sind bei weitem die gebräuchlichsten und stehen daher hier im Mittelpunkt. Obwohl die gelegentliche Goldveredelung oder das Polyimidsubstrat ähnlichen Überlegungen folgen würden. Leider sind diese Materialien und ihre Topographie durch das Produktdesign festgelegt. Die Idee, einen günstigen Kontaktwinkel zu erreichen, indem man sie austauscht, ist nicht realisierbar. Der einzige Punkt, auf den es ankommt, ist die Oberfläche, auf der der Tropfen landet. Die Volumeneigenschaften der Substratkomponenten können gleich bleiben, während die Oberfläche durch Vorbehandlungen die gewünschten Eigenschaften erhält. Bisher hat die Leiterplattenindustrie die Haftung durch Oberflächenvorbehandlungen verbessert. Außerdem erfordert der Tintenstrahldruck eine gute Übereinstimmung mit der Tinte auf der gesamten Leiterplatte. Die Kunst des Herstellers besteht darin, eine solche Übereinstimmung von seinem Lieferanten für Vorbehandlungschemikalien zu verlangen und über nasschemische Anlagen zu verfügen, die die erforderliche Gleichmäßigkeit liefern können. Die Vorbehandlungen, die es im Handel oder in der Entwicklungsphase gibt, haben zwei Gesichter: Entweder kümmern sie sich um das Kupfer und konzentrieren sich darauf, ein Ausbluten zu vermeiden (die Tendenz, einen Kontaktwinkel von fast Null zu bilden), oder sie nehmen die gesamte Platte in Angriff und bereiten eine homogene Oberfläche unabhängig von dem darunter liegenden Material vor, sei es ein Laminat oder Kupfer.
Die erste würde der Tintenstrahltechnologie die Aufgabe überlassen, die Kontaktwinkelunterschiede zwischen z. B. Laminat und Kupfer auszugleichen. Unternehmen bieten diese Technologie heute an (Beispiele in alphabetischer Reihenfolge: Atotech und MEC COMPANY LTD). Die zweite Vorbehandlungsoption mit ihrer zusätzlichen inneren Komplexität erleichtert die Aufgabe der Strukturierung des Tintenstrahldrucks. Unternehmen wie Taiyo bieten solche Vorbehandlungen an. In dieser Anfangsphase der Tintenstrahldrucktechnologie für Lötstoppmasken hat sich noch kein klarer Gewinner für die Vorbehandlungsstrategie herauskristallisiert. Das stimmt, eine neue Zusammenarbeit zwischen zwei Materiallieferanten wurde angekündigt. Viele Kooperationen zwischen Druckfarbenherstellern, Vorbehandlungsanbietern und Ausrüstungslieferanten sind im Gange. Das ist eine gute Nachricht: Das Bewusstsein in der Materiallieferkette ist auf dem richtigen Niveau.
Die Flüssigkeit ist ein einziger Stoff. Eine lohnende Aufgabe ist es, die gemeinsamen Eigenschaften der Materialien zu beschreiben: Die Viskosität der mit dem Tintenstrahldrucker bedruckbaren Lötmaske ist niedrig, niedriger als die der herkömmlichen Lötmaske. Bei Raumtemperatur hat die Tinte eine Viskosität, die etwas höher ist als die von Milch und etwas niedriger als die von Leinsamenöl. Ihre Rheologie bringt weitere Fließeigenschaften wie die Thixotropie mit sich. Inkjet-Tinten sind im Allgemeinen Newtonsche Flüssigkeiten, im Gegensatz zu Standard-Lötstopplacken, die pseudo-plastisch sind (scherverdünnend). Ihre Füllstoffe sind, falls vorhanden, um eine oder zwei Größenordnungen kleiner als bei herkömmlichen Lötmasken. Der integrierte Fotoinitiator ermöglicht eine schnelle und vollständige Polymerisation des Materials. Die letzte bemerkenswerte Makroeigenschaft ist der Gehalt an flüchtigen organischen Bestandteilen (VOC), der je nach Marke und Typ nahe Null oder Null ist. Die letztgenannte Eigenschaft ist die Grundlage für das umweltfreundliche Prinzip dieser Materialien. Nur um das klarzustellen: Nicht nur der VOC-Gehalt ist niedrig, auch das Fehlen von Bebilderungs- und Entwicklungsschritten ist ein klarer Vorteil für die geringe Umweltbelastung durch den Tintenstrahldruck.
Nach einigen Jahren enger Zusammenarbeit mit mehreren Anbietern von Tintenstrahlmaterialien bin ich der Meinung, dass ihr Fahrplan ähnlich sein wird. Zunächst werden diese Anbieter bestrebt sein, die Konformitätsliste innerhalb der IPC-SM-840 und anderer kundenorientierter Normen abzuschließen; einige Anbieter sind weit voraus und andere bereiten ihren ersten Schritt vor. Danach wird jeder die Stärke der von ihm entwickelten Materialien anerkennen und erkunden, wie weit diese reichen können. Ich schließe Allround-Tinte nicht aus.
Beispiele, die den Tintenstrahldruck betreffen, könnten sein: stabile und hohe Kontaktwinkel für feinere Merkmale, Stapelbarkeit für Merkmale mit hohem Seitenverhältnis, Erscheinungsbild jenseits der Farbe (Matt-/Glanzstufen), um die automatische Platzierung optischer Komponenten zu begünstigen, Kombination von abgestimmten elektrischen Eigenschaften und Dickenkontrolle, wie sie der Tintenstrahldruck für extreme RF-Anwendungen (5G und künftige Funkfrequenzen) bietet, extrem niedrige Viskosität für Unterfüllungszwecke, usw.
Sie haben mir also bis hierher gefolgt und wollen nun eine Antwort haben: Welches ist die beste Wahl für mein Lötmasken-Tintenstrahlmaterial? Es ist nicht die Aufgabe dieser Kolumne, eindeutige kommerzielle Präferenzen zu äußern. Mein Ziel ist es vielmehr, einen zeitlosen Leitfaden für die Beurteilung eines Materials und seines Anbieters zu liefern. Ein wesentliches Merkmal eines seriösen Anbieters von Tintenmaterialien ist seine (firmeninterne) Fähigkeit, den Tintenstrahldruck entweder im Labormaßstab oder im Pilotmaßstab zu realisieren. Nur so kann der Tintenlieferant die Bedürfnisse und Herausforderungen seiner Kunden verstehen, wenn sie diese Technologie zum ersten Mal einsetzen. Die Ausrüstungslieferanten haben auch eine unterstützende Funktion, wobei eine gemeinsame Sprache die Grundlage für eine gute Kommunikation ist. Ein weiteres Merkmal ist die Art und Weise, wie sie Inkjet in ihre Roadmap integrieren. Ist Inkjet-Druckmaterial ein zusätzliches Produkt in ihrer Broschüre oder eine Kerntechnologie, die ihr derzeitiges Arbeitspferd irgendwann ersetzen wird? Und schließlich, wie positionieren sie sich auf dem Markt? Meines Wissens haben mehr als eine Handvoll Tintenlieferanten kommerzielle Lösungen (in alphabetischer Reihenfolge: Agfa, Electra Polymers Ltd, MicroCraft K.K, Peters Group, Shenzhen RongDa Photosensitive Science & Technology Co. Ltd., Taiyo America) und mehrere andere Materiallieferanten erwägen den Schritt von der Entwicklung zur Kommerzialisierung. Die Szene wird also immer breiter, was den Fortschritt der Technologie begünstigt.
Die drei Aggregatzustände sind nun durch, obwohl die bisherige Diskussion von einer Annahme ausging: Das Kontaktwinkelgleichgewicht findet lange vor dem Verfestigungsmechanismus durch Polymerisation und Vernetzung statt, die durch UV-Licht induziert werden. In der Zeit zwischen der Kontaktwinkelbildung und dem Verfestigungsmechanismus, etwa hundert Mikrosekunden, dehnt das gedruckte Merkmal seine Kantenfront um ein paar Mikrometer aus. Die Tintenstrahlausrüstung verarbeitet diese Informationen über das Material. Dieses Wissen ist der letzte Schliff, um die Größe des Merkmals genau wie vorgesehen zu erhalten. Dies ist ein Teil der Kunst des "what you see is what you get".
In diesem Artikel wurden mehrere detaillierte Aspekte der Materialien für den Tintenstrahldruck behandelt. Die Lieferkette steckt zwar noch in den Kinderschuhen, aber die kritischen Jahre der anfänglichen Unsicherheit sind vorbei. Interessierte Leiterplattenhersteller werden unabhängig vom Lieferanten ihrer Wahl ein gutes Maß an Kompetenz vorfinden.
Luca Gautero ist Produktmanager bei SÜSS MicroTec (Niederlande) B.V.