L'application du masque de soudure tourne autour du matériau du masque de soudure. Cependant, le matériau ne doit pas être le seul à retenir l'attention. La couche de masque de soudure imprimée par jet d'encre sera constituée d'un ensemble de gouttes ; outre l'encre du masque de soudure, quelques autres matériaux jouent un rôle dans la formation de ces gouttes.
Mon colonne précédente ont accordé une grande attention au positionnement de la goutte. Cependant, au même niveau que le positionnement, ce qui importe est la manière dont la goutte volante, une fois sur le substrat, va atteindre sa forme finale. La section transversale de cette forme (figure 1), et surtout les bords, sont le résultat d'un équilibre. La théorie de l'angle de contact le décrit. Ce qui est intéressant ici, c'est que trois états de la matière sont impliqués et que, par conséquent, un large ensemble de matériaux affecte la goutte. Même un état virtuel, numérique de la matière jouera un rôle.
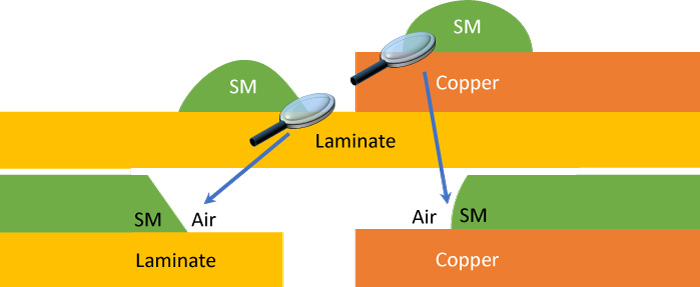
Figure 1 : Croquis montrant des gouttes sur différents matériaux.
La goutte, à l'état liquide, trouve une position d'équilibre sur un solide, le substrat. La prévisibilité de cet équilibre est un paramètre essentiel du jet d'encre. Elle domine la capacité à reproduire un motif avec une grande fidélité. Pour les amoureux de la physique, il existe une abondante littérature qui explique pourquoi, quoi et comment cet équilibre se produit. Dans le cadre de la reproductibilité, il suffit de passer en revue les matériaux impliqués : l'air, le matériau de l'encre et le substrat. Ce dernier devra faire l'objet d'une attention particulière, car chaque substrat varie en topographie et en matière.
L'air est l'élément matériel le plus simple à aborder et ne doit pas être pris pour acquis. L'attention se porte sur les particules en suspension et les courants d'air. Tout d'abord, lorsque par hasard, les gouttes qui précipitent sur la couche de masque de soudure perturbent fortement l'angle de contact. Une considération et deux points d'action permettent d'éviter les problèmes. Seules les particules de grande taille, d'au moins quelques micromètres, créent réellement des problèmes. C'est un soulagement ; des décennies d'expertise de l'industrie des semi-conducteurs sur le contrôle des particules sont disponibles pour gérer de telles tailles.
De la réflexion aux actions : La première action se déroule à l'extérieur de l'imprimante à jet d'encre, un nettoyage humide libère la surface du carton d'arrivée des contaminants, tels que les particules et la contamination organique. La deuxième action consiste à s'assurer que l'environnement interne de l'imprimante a au moins la norme ISO 5 (classe 100). L'absence d'êtres humains dans l'environnement interne simplifie la conception fonctionnelle de cette spécification, car ils constituent la plus grande source de particules. En outre, cette spécification implique qu'un flux d'air propre, lent et homogène, soit présent à tout moment. Ce flux, associé à une conception et à un mouvement appropriés de la tête d'impression, produit des courants d'air prévisibles à l'endroit où la tête d'impression projette les gouttes.
Le solide (substrat) se présente sous plusieurs formes. Les stratifiés et le cuivre sont de loin les plus courants et font donc l'objet du présent document. Cependant, la finition dorée occasionnelle ou le substrat en polyimide suivent des considérations similaires. Hélas, la conception du produit fixe ces matériaux et leur topographie. L'idée d'accommoder un angle de contact favorable en les remplaçant est irréalisable. Cependant, le seul point d'attention est la surface où la goutte atterrit. Les propriétés générales des composants du substrat peuvent rester les mêmes tandis que la surface acquiert les propriétés souhaitées grâce à des prétraitements. Jusqu'à présent, l'industrie des circuits imprimés a amélioré l'adhérence avec des prétraitements de surface. En outre, l'impression à jet d'encre exige une bonne correspondance avec l'encre de manière uniforme sur toute la carte. L'habileté du fabricant serait d'exiger une telle concordance de la part de son fournisseur de produits chimiques de prétraitement et de disposer d'installations chimiques par voie humide capables de fournir l'uniformité requise. Les prétraitements existants, qu'ils soient commercialisés ou en phase de développement, sont de deux types : soit ils s'intéressent au cuivre et s'attachent à éviter les bavures (la tendance à former un angle de contact presque nul), soit ils s'intéressent à l'ensemble de la planche et préparent une surface homogène indépendamment du matériau sous-jacent, qu'il s'agisse d'un stratifié ou d'un cuivre.
La première laisserait à la technologie du jet d'encre la tâche de compenser les différences d'angle de contact entre, par exemple, le stratifié et le cuivre. Des entreprises proposent aujourd'hui cette technologie (exemples dans l'ordre alphabétique : Atotech et MEC COMPANY LTD). La deuxième option de prétraitement, avec sa complexité interne supplémentaire, facilite la tâche de mise en forme de l'impression par jet d'encre. Des sociétés telles que Taiyo proposent de tels prétraitements. Dans cette phase initiale de la technologie d'impression à jet d'encre pour les masques de soudure, un vainqueur clair pour la stratégie de prétraitement n'est pas encore apparu. En effet, une coopération récente entre deux fournisseurs de matériaux a été annoncé. De nombreuses collaborations entre fabricants d'encres, fournisseurs de prétraitement et fournisseurs d'équipements sont en cours. C'est une bonne nouvelle : la prise de conscience est au bon niveau dans la chaîne d'approvisionnement en matériaux.
Le liquide est un matériau unique. Un exercice intéressant consiste à décrire les propriétés communes des matériaux : La viscosité du masque de soudure imprimable par jet d'encre est faible, inférieure à celle du masque de soudure traditionnel. À température ambiante, l'encre aurait une viscosité un peu plus élevée que le lait et un peu plus faible que l'huile de lin. Leur rhéologie fait intervenir d'autres caractéristiques d'écoulement telles que la thixotropie. Les encres pour jet d'encre sont généralement des liquides newtoniens, contrairement au masque de soudure standard qui est pseudo-plastique (fluidification par cisaillement). Leurs charges sont, si elles sont présentes, d'un ou deux ordres de grandeur plus petites que dans le masque de soudure traditionnel. Le photo-initiateur intégré permet une polymérisation rapide et complète du matériau. Enfin, la dernière macro-propriété notable est la quantité de composants organiques volatils (COV) qui est proche de zéro ou nulle selon la marque et le type. Cette dernière propriété est à la base du principe de respect de l'environnement de ces matériaux. Pour être clair, il n'y a pas que les COV qui sont faibles, l'absence d'étapes d'imagerie et de développement sont des avantages évidents dans le faible impact environnemental de l'impression à jet d'encre.
Après quelques années de travail étroit avec plusieurs fournisseurs de matériaux pour jet d'encre, mon opinion est que leur feuille de route sera similaire. Tout d'abord, ces fournisseurs s'efforceront de finaliser la liste de conformité dans le cadre de la norme IPC-SM-840 et d'autres normes définies par les clients ; certains fournisseurs sont très en avance et d'autres préparent leur coup de départ. Ensuite, chacun d'entre eux reconnaîtra la force du ou des matériaux qu'il a développés et explorera jusqu'où ils peuvent aller. Je n'exclus pas l'encre universelle.
Les exemples qui concernent l'impression par jet d'encre peuvent être les suivants : angles de contact stables et élevés pour les caractéristiques plus fines, empilabilité pour les caractéristiques à rapport d'aspect élevé, aspect allant au-delà de la couleur (niveaux de matité/brillance) pour favoriser le placement automatique des composants optiques, combinaison de propriétés électriques accordées et contrôle de l'épaisseur tel que fourni par le jet d'encre pour les applications RF extrêmes (5G et futures radiofréquences), viscosité extrêmement faible à des fins de sous-remplissage, etc.
Donc, vous êtes resté avec moi jusqu'ici, et maintenant vous voulez votre réponse : Quel est le meilleur choix pour mon masque de soudure à jet d'encre ? Ce n'est pas le rôle de cette chronique de faire des préférences commerciales explicites. Mon objectif est plutôt de fournir un guide intemporel sur la manière d'évaluer un matériau et son fournisseur. L'une des caractéristiques essentielles d'un fournisseur d'encre sérieux est sa capacité (interne) à mettre en œuvre l'impression par jet d'encre, que ce soit à l'échelle du laboratoire ou à un niveau pilote. Ce n'est que de cette manière que le fournisseur d'encre comprendra les besoins et les défis de ses clients lorsqu'ils mettent en œuvre cette technologie pour la première fois. Les fournisseurs d'équipements ont également un rôle de soutien, bien qu'un langage commun soit la base d'une bonne communication. Une autre caractéristique est la manière dont ils intègrent le jet d'encre dans leur feuille de route. Le matériel d'impression à jet d'encre est-il un produit supplémentaire sur leur brochure ou une technologie de base qui remplacera un jour leur cheval de bataille actuel ? Enfin, comment se positionnent-ils sur le marché ? À ma connaissance, plus d'une poignée de fournisseurs d'encre ont des solutions commerciales (dans l'ordre alphabétique : Agfa, Electra Polymers Ltd, MicroCraft K.K, Peters Group, Shenzhen RongDa Photosensitive Science & Technology Co. Ltd. et Taiyo America) et plusieurs autres fournisseurs de matériaux envisagent de passer du développement à la commercialisation. La scène s'élargit donc, ce qui favorise le progrès de la technologie.
Les trois états de la matière sont maintenant terminés, même si la discussion menée jusqu'ici reposait sur une hypothèse : l'équilibre de l'angle de contact se produit bien avant tout mécanisme de solidification par polymérisation et réticulation induite par la lumière UV. Pendant le temps qui s'écoule entre la formation de l'angle de contact et le mécanisme de solidification, soit environ une centaine de microsecondes, l'élément imprimé élargit son front de quelques micromètres. L'équipement à jet d'encre traite cette information sur le matériau. Cette connaissance est la touche finale pour obtenir la taille de l'élément exactement comme prévu. Cela fait partie de l'art du "what you see is what you get".
Cet article a abordé plusieurs aspects détaillés des matériaux utilisés dans l'impression à jet d'encre. La chaîne d'approvisionnement n'en est qu'à ses débuts, mais les années critiques d'incertitude initiale sont passées. Les fabricants de PCB intéressés trouveront un bon niveau de compétence indépendamment du fournisseur de leur choix.
Luca Gautero est chef de produit chez SUSS MicroTec (Netherlands) B.V.